McLeod Cranes overhauls manual systems with Slack
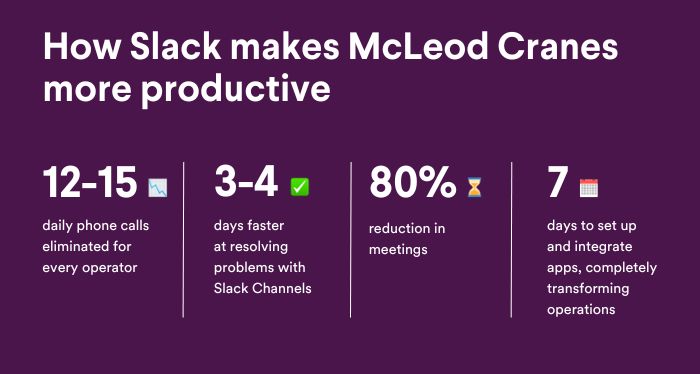
For McLeod Cranes, a New Zealand-based crane, hiab and transport business, a day at work looks different to your typical office job. Most work happens offsite, and 80% of its employees have no access to a computer.
But as McLeod Cranes expanded its business, its old pen-and-paper processes were not keeping up.
McLeod Cranes needed an efficient and integrated platform to dispatch cranes and operators on time, keep maintenance data up to date and ensure site safety. That’s why it turned to Slack.
Slack integrations lift site safety and cut costs
For McLeod Cranes, site inspections are a vital part of any job. They help determine which assets are required, how operators should access a site, and detail any safety considerations.
McLeod Cranes’ old way of doing site inspections was manual. Paper forms were filled out and filed, but had a way of going missing.
“Before Slack, everyone was looking for a workaround. We tried email, WhatsApp, Google chat, and Facebook to send photos and videos to dispatchers, but there were limits,” says Rob Curtis, a Hiab Operator at McLeod Cranes. “Sometimes, it was easier just to drive back to the office to share pictures in person.”
To streamline this process and make life easier for its operators, McLeod integrated its dispatch software vWork with Slack.
Each inspection now automatically generates a Slack channel, creating an accessible, searchable history for a job that includes vital photos and site details.
McLeod Cranes Managing Director Scott McLeod set up the vWork integration himself in just a few days, using Slack’s drag-and-drop, low-code integrations.
“Slack is the ‘killer app’ that provides us one single platform to operate, including the guys in the field who only have access to a mobile phone,” says McLeod.
Since switching to Slack, operators are arriving at sites better prepared and are saving themselves 12 to 15 phone calls to dispatch a day. Jobs get done faster and with less rework.
“Since moving to Slack, quality has increased, complaints are down, and fewer invoice changes are needed. This doesn’t just save time—it directly affects dollars,” says McLeod.
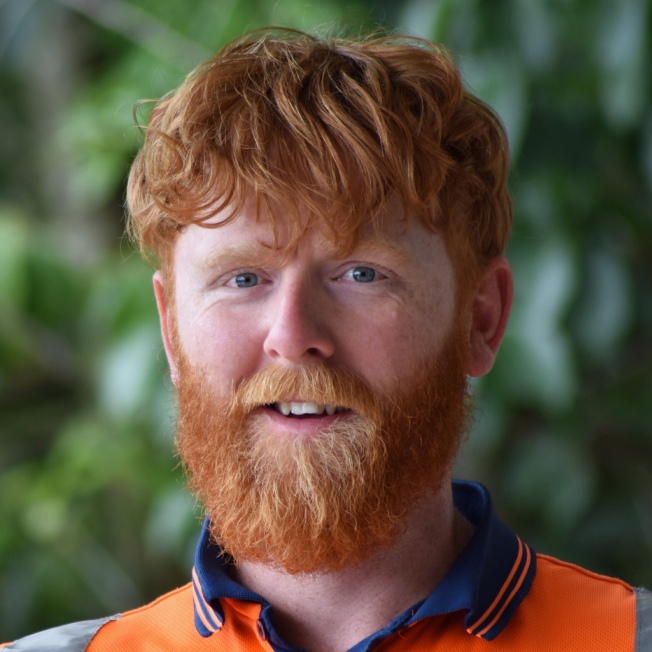
“Before Slack, everyone was looking for a workaround. We tried email, WhatsApp, Google chat and Facebook, but there were limits. Sometimes, it was easier just to drive back to the office to share pictures in person.”
Automated event reports speed up health and safety responses
McLeod Cranes’ health and safety event reporting has also been streamlined thanks to Slack integrations.
With Slack, McLeod Cranes’ built a “no blame” reporting system that’s designed to encourage operators to report events and get them help quickly.
Within minutes of an event being reported, a “cleaned” incident report is automatically sent to the health and safety team in a Slack channel.
A ChatGPT integration with Slack removes the operator’s name and blame, rates the event, and summarises the top 3 details needed to take swift action.
The operator also receives an automated Slack message to remind them of immediate safety actions like isolating the area or taking photos.
“Humans miss things, Slack doesn’t. We’re seeing a curve in reversing events since integrating events reporting with Slack,” says McLeod.
Taking maintenance reports out of silos and into Slack channels
Accessing maintenance reports used to be a struggle for McLeod Cranes’ operators. They were sent as emails, meaning there was no quick and easy way to view a log of repairs for each asset.
This problem was fixed when McLeod Cranes integrated its Gearbox maintenance management system with Slack.
Now, maintenance reports are automatically created and updated in Slack channels for each asset, saving valuable time for crane and hiab operators. Everyone is kept up to speed, even when working different shifts.
“It only took 2-3 hours to integrate our asset maintenance with Slack. A problem that seemed unsolvable was fixed overnight,” says McLeod.
Solving business problems faster (and with fewer meetings)
One of the biggest time-wasters for any business is too many inefficient meetings. Before Slack, McLeod Cranes’ operations were no exception.
“Thanks to Slack, I’m down from five meetings to just one. Meetings used to be a lot of talk and little action. Now, we pull up a Slack Canvas with action items and then tick them off immediately,” says McLeod.
With everything shared in Slack channels, management can see problems emerging and react faster without the need to call meetings.
This more transparent way of working is helping McLeod make better decisions about resourcing and the direction of the business as a whole.
“With Slack, what used to take 3-4 days to understand and resolve now takes me a minute.”